2017精益质量管理论文
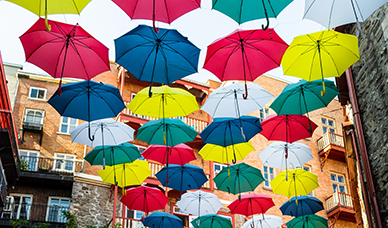
一个企业在未来能够走多远,取决于企业的精益质量管理是否能够得到市场的认可与信赖,小编整理了2017精益质量管理论文,欢迎阅读!
2017精益质量管理论文篇一
装配过程精益质量管理应用研究
摘要:产品装配作为制造过程的最后一个也是最为重要的环节之一,其质量对于产品质量有着重大影响。在产品装配环节应用精益质量管理理念综合改善装配的质量、效率和成本是质量管理新的发展趋势。分析精益质量管理,围绕装配过程质量管控的各个环节,通过对装配过程履历表的电子化的存储,质量缺陷的分析预测和关键零件的优化匹配,显著提高了企业装配过程的质量绩效和经营绩效。
关键词:装配过程;质量管理;履历表;质量缺陷;关键件
一、引言
装配既是产品制造的最后一个环节,也是产品生命周期的重要组成部分,是实现产品功能的主要制造过程。纵观质量管理百年历程,经历了传统质量检验、统计质量控制、全面质量管理几大阶段,目前以六西格玛管理为核心的精益质量管理正成为质量管理新的发展趋势。本文针对企业存在的问题,应用精益质量管理的理念,围绕装配过程质量管控的各个环节,采用数字化手段来改造传统的制造方式,提升产品质量,实现企业利润最大化。
二、精益质量管理
精益质量管理是借鉴丰田公司精益生产、六西格玛管理和iso9000质量体系的实践经验,结合我国企业管理实践形成的理念和方法精华,是在对关键质量数据的定量化分析基础上,综合运用多种知识和方法,对关键质量指标持续系统改进,追求达到卓越标准,以实现显著提高企业质量绩效及经营绩效的目的,是企业提高经营绩效的重要战略。
然而,目前我国大多数企业在装配过程中的质量控制仍比较落后,严重影响了装配质量的提升和企业的质量绩效。
三、履历表的电子化
精益质量管理的基本任务就是通过对质量数据进行分析,对系统进行综合改善,最终实现企业。其中质量数据是装配质量检验信息的统计、分析和质量趋势预测的基本依据。而传统的质量数据是通过纸质履历表的形式体现出来,在质量管理中,检验记录被存储在产品或零部件的履历表中,每件产品包含大量的零部件的履历表,这些履历表被分散在各个环节流通和保存,容易造成质量数据的丢失和不完整,也不利于分析和及时的消除异常情况。
因此,可通过将存储质量数据的履历表进行电子化的手段,实现质量数据的集中、有序管理,为查询、统计和分析预测提供依据。针对装配过程履历表结构特征进行分析,采用通用的电子表格管理的数据结构,将信息表格分为模板、样式、网格、列等四种基本元素,其中每个样式由多个格网组成,每个格网又由多个列数组成,最终实现质量信息的结构化建模和存储,为用户提供能够描述各种质量信息表格的工具。通过这个工具,可以为样式添加模板数据,并为格网定制行数,形成表单模板,再在模板中添加实际数据就得到了实际表单,从而实现了质量检验表单的电子化。
四、质量数据的分析预测
在装配制造过程中,由于涉及零部件数目繁多,业务流程复杂,错装、漏装等问题经常发生,严重影响了装配质量和生产效率,需要对装配质量缺陷进行分析和预测,形成质量检验的经验数据,为装配操作和检验分析提供警示和提示信息,从而减少浪费,实现质量、效率和成本的综合提升。
对于装配过程质量缺陷的分析和预测,其方法可分为两种:一是基于粗糙集理论实现装配故障的诊断、学习,提高装配质量,此类方法的特点就是不需要任何装配过程失误数据的支持,可自行学习和分析出质量问题的原因,从而指导装配过程;二是传统的方法,就是通过对装配过程中的质量失误进行分析,建立与设计复杂性、工艺复杂性的关联,从而实现装配质量事故的统计预测;也可以提供装配过程中的数据,进行主分量分析和聚类分析,对装配质量进行评估,改善生产和装配过程的监控手段,提高生产效率。
五、质量关键指标的优化
对于装配制造过程,经常出现的一个质量问题是配合件之间的配合误差不能满足设计要求,通过分析发现其问题的根源在于装配制造环节上游(如机加等)过程中出现的各种质量问题(如超差等),但考虑到经济性和加工水平的因素,需要在装配制造环节进行解决。因此,在装配过程中,需要通过零件选配的方法消除此类误差,而传统的选配方法是试装、测量,若不合格则拆卸、选件、再装配、再测量,这种方法耗费大量人力和工期,不一定能装出合格且精度较高的部件。
为了解决此类问题,对于结构复杂、装配尺寸精度要求高的产品装配,研究计算机辅助选配,在各组成环零件按经济加工精度的条件下,对各组成环偏差进行合理匹配,缩小封闭环偏差的变动范围,提高装配制造过程的生产效率和产品质量一致性。在实施中的关键步骤包括:对关键件及其尺寸进行标识、测量和记录;构造出通过关键件关键尺寸计算出关键配合尺寸模型;依据关键件关键配合尺寸模型,结合关键件实测数据,采用基于多目标优化遗传算法的优配算法,计算出当次发料所需台份的关键件配合清单。
六、展望
装配质量对于产品质量有着重大影响,在装配过程中利用先进的制造技术实现产品的效率、质量和成本的全面提升是一个新的研究课题。本文应用了精益质量管理的理念,提出了装配过程中三类典型质量问题的改善方案,但对于精益质量管理理念的应用还不够深入,对于精益质量管理所推行的作业标准化,度量精细化等还需要进一步的研究。
参考文献:
1、常智勇.装配制造数字化研究综述[j].航空制造技术,2008(11).
2、走近精益质量管理[j].中国质量技术监督,2007(7).
3、常智勇,赵杰.复杂产品装配执行过程数字化技术[j].南京航空航天大学学报,2009(10).
4、吕琳.数字化制造技术国内外发展研究现状[j].现代零部件,2009(3).
5、宋文龙.基于多装配尺寸链的计算机辅助选择装配[j].现代制造工程,2007(4).
(作者单位:西安航空技术高等专科学校机械工程系)
点击下页还有更多>>>2017精益质量管理论文
- 共2页:
- 上一页
- 1
- 2
- 下一页
2017精益质量管理论文篇二
践行精益理念、提升质量管理
[摘 要]随着市场经济的快速发展,企业之间的竞争越来越激烈,一个企业在未来能够走多远,取决于企业的产品质量是否能够得到市场的认可与信赖,因此严把产品质量关是立足市场的基本条件。产品质量不仅仅是一个产品的使用寿命,它是一种综合评定,是企业的立足之本。本文从精益管理的理念出发,阐述精益质量管理的方法以及在现场中的实际应用。
[关键词]精益 理念 质量 管理
中图分类号:c93 文献标识码:a 文章编号:1009-914x(2016)11-0164-01
fullfill the concept of lean production ,improve quality management
zheng xin
(csr zhuzhou electric co.,ltd,zhuzhou 412001,china)
[abstract]as rapid developement of market economy ,the competition of enterprise is more and more fierse. how long a enterprise can live depend on its quality.the quality of products is not only its life length, but also a comprehensive evaluate and basis of a enteprise.the thesis declare the method of qualitu management and its appliance from te concept of lp.
[key words]lean production caoncept quality management
前言
随着现代各种先进管理思想的发展和应用,精益思想也在质量管理方面获得了发展,并逐渐形成了精益质量管理。精益管理强调质量是生产出来而非检验出来,众所周知在产品生产过程的质量控制中,更多的是需要生产一线的操作人员来完成,如何实现生产操作人员的自我质量控制,是各级管理人员长期工作努力的努力方向,也是实现产品质量提升的关键因素。精益管理思想更多的是一种源头的改善思想,在质量管理中体现的就是在哪里产生问题就在哪里予以消除,从而实现对产品质量的事前、事中预防与控制。
1 精益质量管理的特点
1.1工作流程标准化。标准化的工作流程是企业实施精益质量管理的基础,一切工作都应按照流程标准来完成,不清晰的流程更容易导致问题的出现,只有在任何情况下都坚持流程的标准化操作,才能更好地提高企业的效率,增强质量管理能力。
1.2生产管理系统化。精益质量管理很重视生产系统的管理,从产品的生产过程中发现并解决影响产品质量的问题。精益质量管理利用精益生产中的6s管理、目视化等工具保证了生产系统有条不紊地运作,并通过利用各种方法对产品质量信息的分析,找到并解决影响产品质量的各种因素。
1.3产品质量零缺陷化。精益质量管理借鉴了精益生产中对产品质量零缺陷的要求,这就要求全体员工始终将“零缺陷”作为工作的标准,对任何一道工序都精益求精,在第一次操作的时候就将事情做好,不放过任何一点小问题,保证产品品质的零缺陷。
1.4质量改进持续化。持续的质量改进是is09000:2000版标准给出的八项质量管理基本原则之一,也是精益思想、全面质量管理重点关注的化的工作流程是企业实施精益质量管理的基础,一切工作都应按照流程标准来完成,不清晰的流程更容易导致问题的出现,只有在任何情况下都坚持流程的标准化操作,才能更好地提高企业的效率,增强质量管理能力。
2 精益质量管理的方法及应用
2.1让不良品表面化。精益生产管理认为任何不良的出现,必定有其内在的原因,只有解决了发生不良的各项原因,才能真正的实现零缺陷,才能让客户真正满意。如果按照传统的思维和做法由作业者对不合格品自行返工或报废,那么下次还会发生同样的问题。因此要设置专用的不合格品展示台,不间断地展示不合格品,针对不合格品产生的原因和应采取的对策由现场人员对操作工序逐个分析,提高每个员工的辨别识别能力,转变其对不良的态度。
2.2发现异常状况要立即停机。精益生产管理强调能够实现“自动化系统”(即能停止的生产系统),保证能够停止生产。在精益生产管理中任何原因造成的停止都会作为头等大事对待,都会成为全员关注的焦点。停机将使所有的现场支援者快速处理问题,针对原因制定出切实可行的再发防止对策。这其中因品质不良造成的停机是首要的,只有实现停机才能保证生产现场不放过任何一个不良品。
2.3操作者必须实施全数检查。“零缺陷”的实现必须由操作者自己完成100%的检查,要求操作者将下道工序作为自己的客户看待,只向后工序输送合格品。 检验工的职责不是将不合格品检出,而是将不合格品降低为零。因此作为工序作业控制的一部分必须要求操作者实施全数检查。
2.4充分使用放错装置。在生产过程中,操作者受各种客观因素的影响终有失误的时候,有些人为的错误是不可避免的。如果将品质水平依赖于人的工作态度,则品质仍不能有效保证。但是我们可以设计出这样的装置,不给操作者犯错的机会,这样就是精益生产管理普遍使用的放错装置。如作业忘记或失误时,机器不能启动。操作过程失误时报警装置鸣叫,设备停止;出现加工错误时,生产线会阻挡不良的工件,不流到下工序等等。
2.5生产和作业平准化。平准化包括数量平准和品种平准。平准话生产后,由于流程中在制品数量急剧减少,造成搬运动作的减少、码放动作的减少等,这些都会减少由于磕碰、挤压而产生的不良。同时由于工件减少使得产品错装、漏装、多装等情况也不会发生,这样由于生产作业是在有规则和平稳的状况下运行的,错误作业发生的可能性得到大幅度下降。
2.6执行标准化作业。标准化作业是彻底消除作业浪费,使操作者的作业规律化、定期化。标准化作业以在现场不生产不良品为出发点,也是改善的出发点和维持点。同时标准化作业也为培养新人和生产标兵提供有效保证。
3 结束语
总之,精益生产管理是控制不良品的制胜法宝,带给大家一种双赢的思想理念,其精髓是解决问题、消除浪费,实现品质零缺陷的跨越。同时,坚持精益质量管理改善持续化,强调以客户的需求为中心、全员参与,并结合全面质量管理的理念,对生产过程中的质量进行持续改善和提升。
参考文献
[1] 嵇国光,《现场精益质量管理》,中国标准化出版社,2014.
[2] 鲁克德,《胜在制度,赢在执行》,立信会计出版社,2012.
[3] 山西省水利水电勘测设计研究院,《精益化技术质量管理》,水利水电出版社,2011.
[4] 杨彬,《精益生产管理与实施》,北京高教音像出版社,2010.
[5] (美)彼得.德鲁克,《精益质量官》,金城出版社,2012.
看了“2017精益质量管理论文”的人还看:
1.精益质量管理论文
2.精益质量管理论文(2)
3.精益生产管理论文
4.精益安全管理论文
5.关于精益管理心得体会
- 共2页:
- 上一页
- 1
- 2
- 下一页

上一篇:建筑企业运营管理论文
下一篇:公共组织人力资源管理论文